Bulletin
Dear Stakeholders,
As we leave 2024 behind, we have witnessed significant developments both in our country and globally. Despite going through tough times, we managed to keep our hopes and goals alive. International tensions and economic challenges deeply affected us all. However, we overcame these difficulties and managed to move forward stronger than before. Despite all these challenges, 2024 has been a year full of successes for our company, achieving the goals we set at the beginning of the year.
As Nurol Teknoloji, we reached important milestones in 2024. We further strengthened our leadership in the defense industry, continued to create innovative solutions, and made strategic investments. With the solutions we offer in the fields of ballistic ceramics and armor systems, we continued to provide uninterrupted service to domestic security forces and our business partners around the world.
As one of the leading companies in the Turkish defense industry, we continued to make a difference in security through the solutions we offer to our global clients. Our high-quality and high-value ballistic protection products, offered under the NT Armor and NT Cera brands by our company, Nurol Technology USA, in America, received great acclaim from our customers. In line with our goal to increase our presence internationally, our vertical integration, strengthened by the acquisition of the German company Industriekeramik Hochrhein (IKH), has highlighted our industry experience and capacity advantages, allowing us to continue providing the highest quality service to meet the growing demand.
As we step into 2025, we move forward with even greater goals. We will strengthen our technological infrastructure and solidify our position in the industry with new projects. With the principle of serving humanity and protecting the good, we will continue to add value to society and the industry. I wish the new year brings health, success, and peace to all our stakeholders, and I look forward to achieving even greater success together in 2025.
Sincerely.
Selim BAYBAŞ CEO – Board Member
Nurol Teknoloji: Crowned 2024 with Global Success, R&D, and Strategic Investments
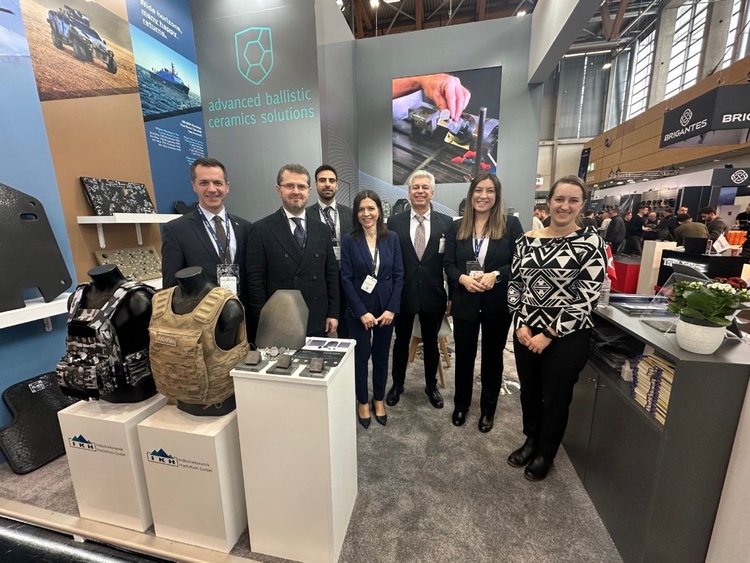
The year 2024 has gone down in history as a challenging year on a global scale. Wars, conflicts, terrorist attacks, and issues affecting the supply chain due to physical and political embargoes around us forced us all into a major struggle. However, as Nurol Teknoloji, despite all the challenges we faced, we managed to overcome this process by producing flexible and rapid solutions. By overcoming the obstacles in the supply chain, we successfully delivered our customers' needs on time and with the expected quality. This process not only showcased our operational strength but also highlighted our strong collaborations and crisis management experience. While overcoming these difficulties, we always prioritized customer satisfaction.
2024 marked a significant milestone for Nurol Teknoloji in the field of R&D. The acquisition of IKH allowed us to increase our research and development capacity, providing a great opportunity to produce innovative solutions. As a result of our intense R&D efforts, we developed advanced technical ceramic powders and successfully introduced the next generation of advanced technical ceramics made from these powders to the market. Our new-generation ceramics received great interest internationally. Currently, our ballistic protection products developed with these unique ceramics, which are not found anywhere else in the world, are making a significant impact in the industry in terms of both performance and lightness.
Five of our products were certified by the American National Institute of Justice (NIJ) authority. Nurol Teknoloji became the only Turkish company with products holding this prestigious certification. Additionally, these products were licensed by 12 of the leading companies in the ballistic armor sector in the United States.
2024 was not only a year of advancements in R&D but also saw important steps in production and infrastructure investments. With new press, furnace, and equipment investments, we doubled our production capacity. These investments helped us create a strong infrastructure to meet higher demands, not only in the domestic market but also internationally. With our increased capacity, we met the high-volume needs of Turkish security forces. We also responded to the demands of NATO countries, other allied countries' armed forces, and security forces across a wide region from Asia to the Gulf.
Nurol Teknoloji continued to develop personal protection products and vehicle armor, collaborating with vehicle manufacturers to integrate these armors. 2024 was particularly focused on armored vehicle protection for high-threat levels, as well as the mass production of the lightest boron carbide helicopter armors.
2024 was a year of not only operational achievements but also important steps taken to improve and develop our company. As Nurol Teknoloji, we earned the TURQUALITY® certification, a state-supported branding program that helps Turkish companies become global players with their own brands in international markets, supporting their development in all processes from production to marketing. This certification became an important milestone, elevating us to a strong position not only in the local market but also on the global stage.
Moreover, by further developing our unique ballistic analysis and simulation infrastructure, we reinforced our leadership in the sector. We shared our work with our stakeholders at the world's most prestigious conferences in the field of ballistics. During our digital transformation journey, we expanded Jarvis, created digital twins of our ceramic and composite excellence centers, and achieved a more efficient production process. Every day, we became more digital, more traceable, and more efficient, reaching operational excellence.
In achieving all these successes, we once again proved that our greatest strength lies in our qualified workforce and that working with the best people is essential to continue protecting the best. We enter 2025 with the same determination. Meeting our customers' needs in the best and fastest way, continuing R&D efforts, and constantly improving our company will be our top priorities. While continuing our operations in line with our vertical integration strategy, we will strengthen our strategic collaborations and increase our global footprint, achieving even greater success.
May the new year be healthy, happy, and full of success for all of us!
Best regards.
Serpil GÖNENÇ DİNÇER / Commercial Deputy General Manager
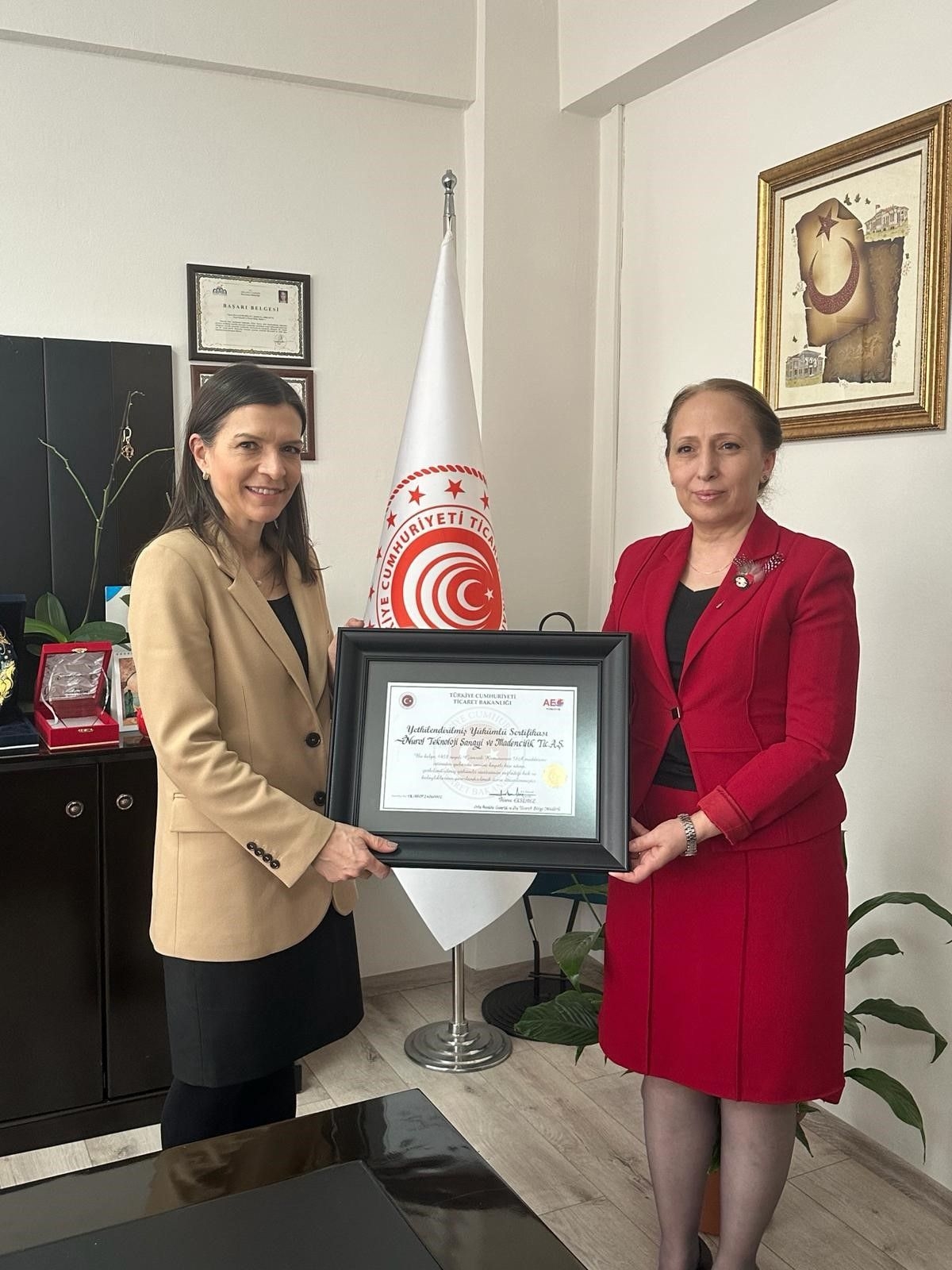
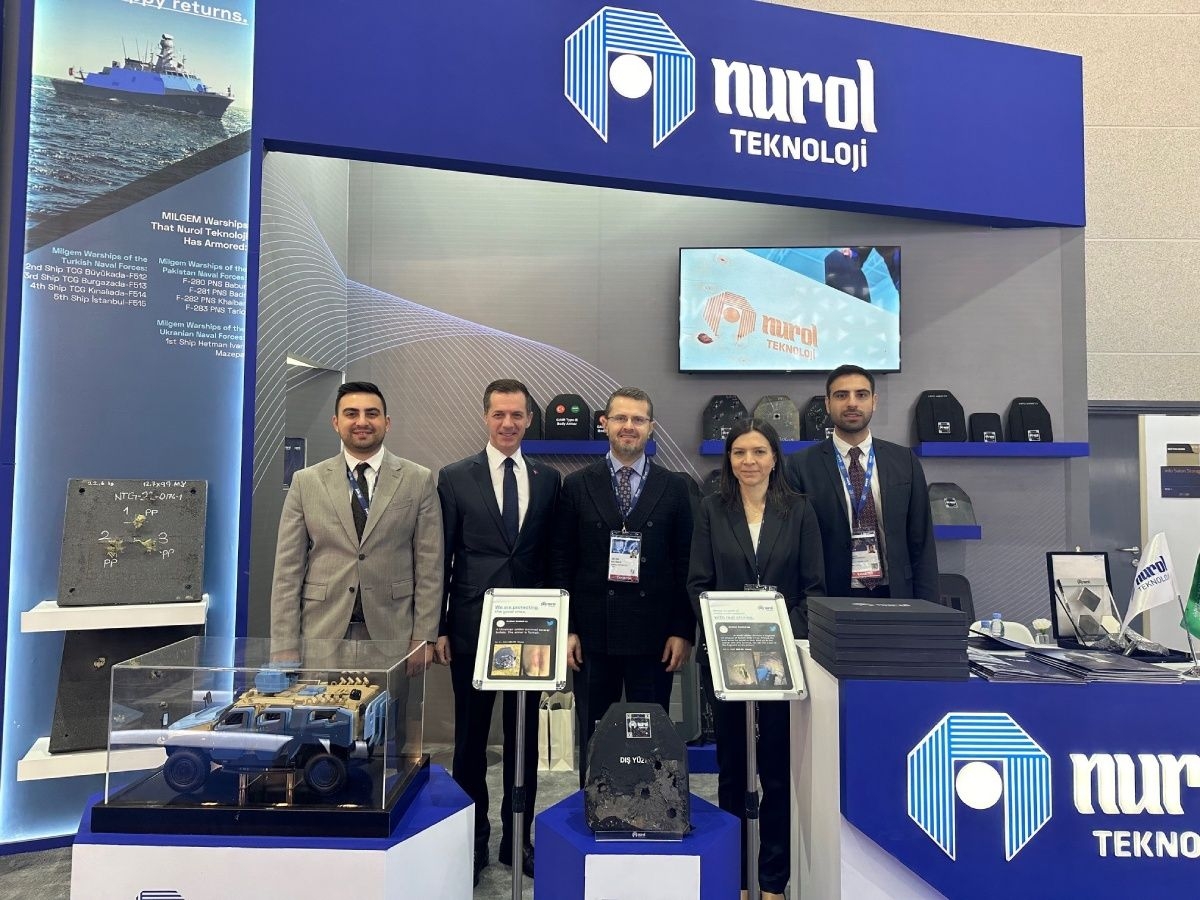
Advanced Simulation and Innovative Manufacturing Methods in Armor Technologies
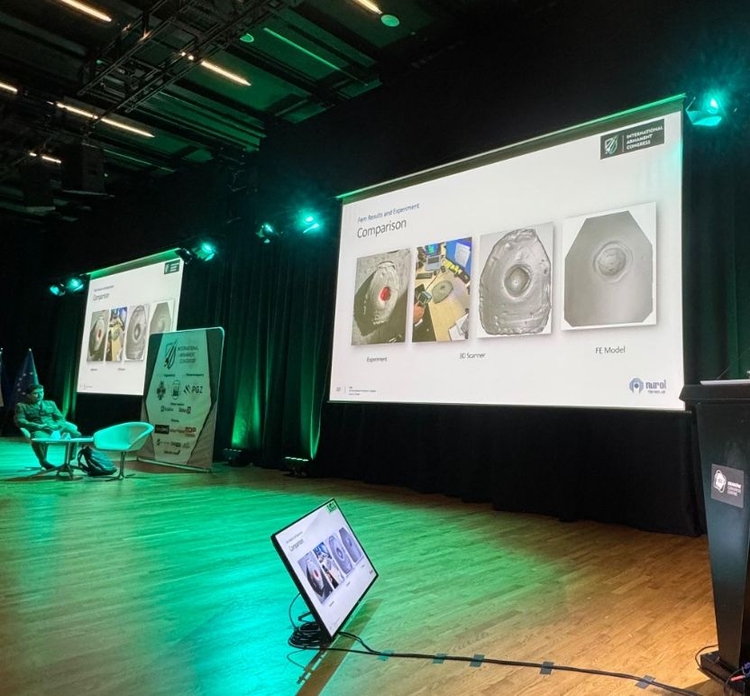
Our process for conducting ballistic simulations of armor with various protection levels symbolizes a breakthrough in engineering. We test the performance of each armor not only with experimental data but also in a digital environment using finite element models. With advanced modeling techniques, we thoroughly investigate the dynamic interactions, energy dissipation capacities, and ammunition erosion in each layer of the armor. Through real-time simulations, we accurately measure the complex interactions between ballistic projectiles and armor, optimizing the design process at every stage. As a result, we not only provide high levels of protection but also offer the most efficient solution in terms of the armor's lightness and durability.
In our terminal ballistic simulations, we achieved a significant transformation with the Split Hopkinson Pressure Bar (SHPB), which has both tensile and compressive modes. This innovative tool allows us to understand the behavior of materials under dynamic loading, while measuring the mechanical properties of materials interacting at high speeds, which has increased the accuracy of our finite element models from 85% to 92%. Additionally, we have developed a quality control standard for our self-developed ceramic materials. We systematically compare the performance of ceramics produced with different formulations under dynamic loading. This approach allows us to not only evaluate the performance of our ceramics in ballistic or static tests but also determine the most efficient ceramic formulation at different impact speeds.
We do not keep our innovative computational engineering approaches within the company, but also share them with the international academic ballistic community. In this context, we presented our work titled "Correlative Analysis of Behind Armor Blunt Trauma on Body Armor With Real Ballistic Test Campaigns", where we examined the backface trauma values of ceramic-based personal armors using both real ballistic tests and finite element methods, at the "International Armament Congress" held in Krakow, Poland, from October 21-25, 2024.
Cold pressing plays a significant role in the production of ceramic-based armor applications. In this context, the modeling of ceramic cold pressing manufacturing methods using computational mechanics and the importance of simulation studies for different pressing conditions come to the forefront. The TEYDEB 1505 project titled "Optimization of Ceramic Powder Layering Topology for Chest Plate", developed by the Nurol Technology Analysis and Simulation R&D Unit, has been accepted for support by TÜBİTAK and is targeted to be completed between 2025 and 2026. With this project, the cold pressing stage of manufacturing will be quantitatively modeled using computational solid mechanics methods, pressing parameters will be determined to achieve a uniform distribution of density within the plate, and optimization of the powder layering topology and the design of the appropriate sieve will be carried out.
Producing samples with dimensions close to the final shape in ceramic products is a complex process that requires advanced calculations. Ceramic powders with different characteristics in terms of shrinkage or expansion make it challenging to achieve the desired dimensions in the final product, especially in cases involving curved geometry and loading conditions. Moreover, even products made from samples taken from different production campaigns of the same powder type can exhibit varying final product dimensions. To manage this process in a controlled and traceable manner, the Nurol Technology Ceramic R&D Unit has developed a data-driven statistical model. With this model, the final dimensions of ceramic-based armor plates are predicted within specific tolerance limits, significantly increasing ceramic production yields. As the Nurol Technology R&D Unit, we have integrated the software we developed in-house into the production process. This software provides the required measurement data for the product geometry after cold pressing, which the final product must meet, in graphical and tabular form to the user. These data are shared with the production team to guide the manufacturing process.
Among our goals for 2025, we aim to integrate adjustable designs into our cold press equipment with dosing systems. These innovative designs will allow us to precisely control the material quantity while adapting to the different tolerance requirements of each project. Additionally, the dosing system will accelerate production processes, enabling higher efficiency with less material waste. Through all these innovative approaches, we aim to continuously improve production quality while enhancing flexibility and effectiveness in our projects.
Best Regards.
Koray KAYA / Analysis and Simulation Chief
Halim MEÇO / Advanced Technical Materials R&D Director
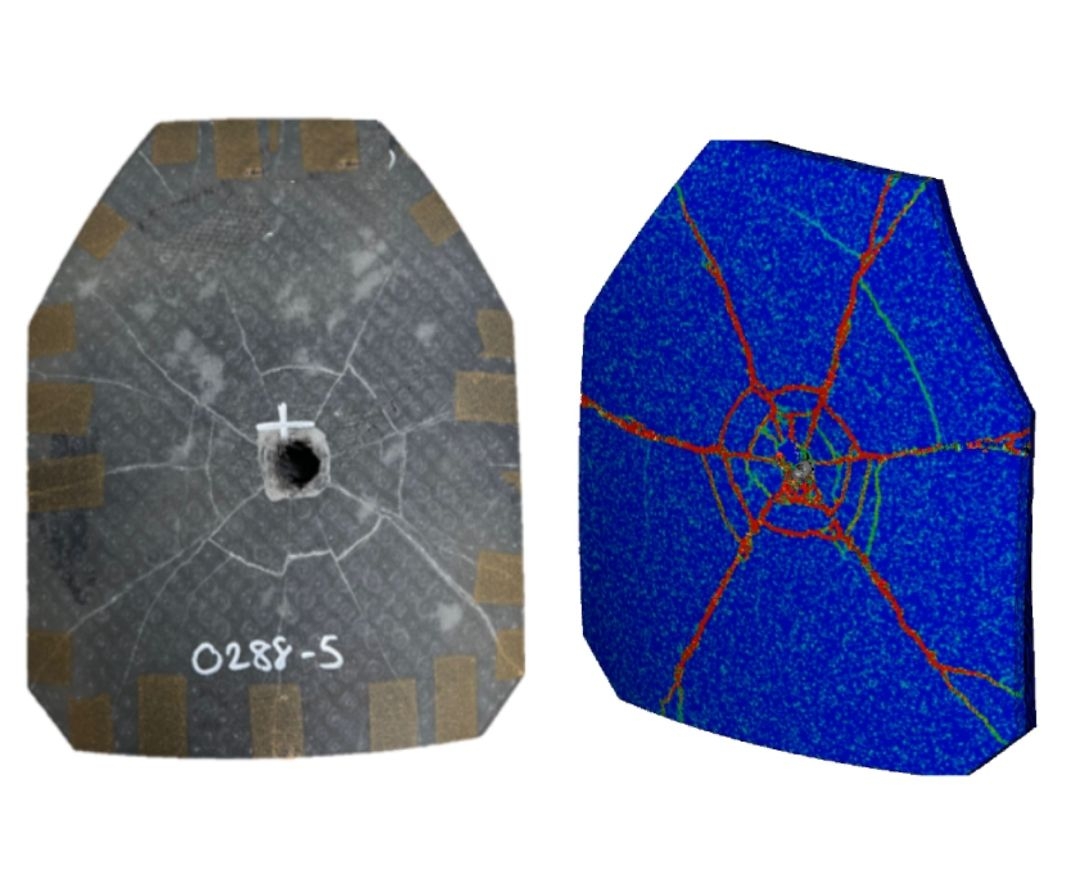
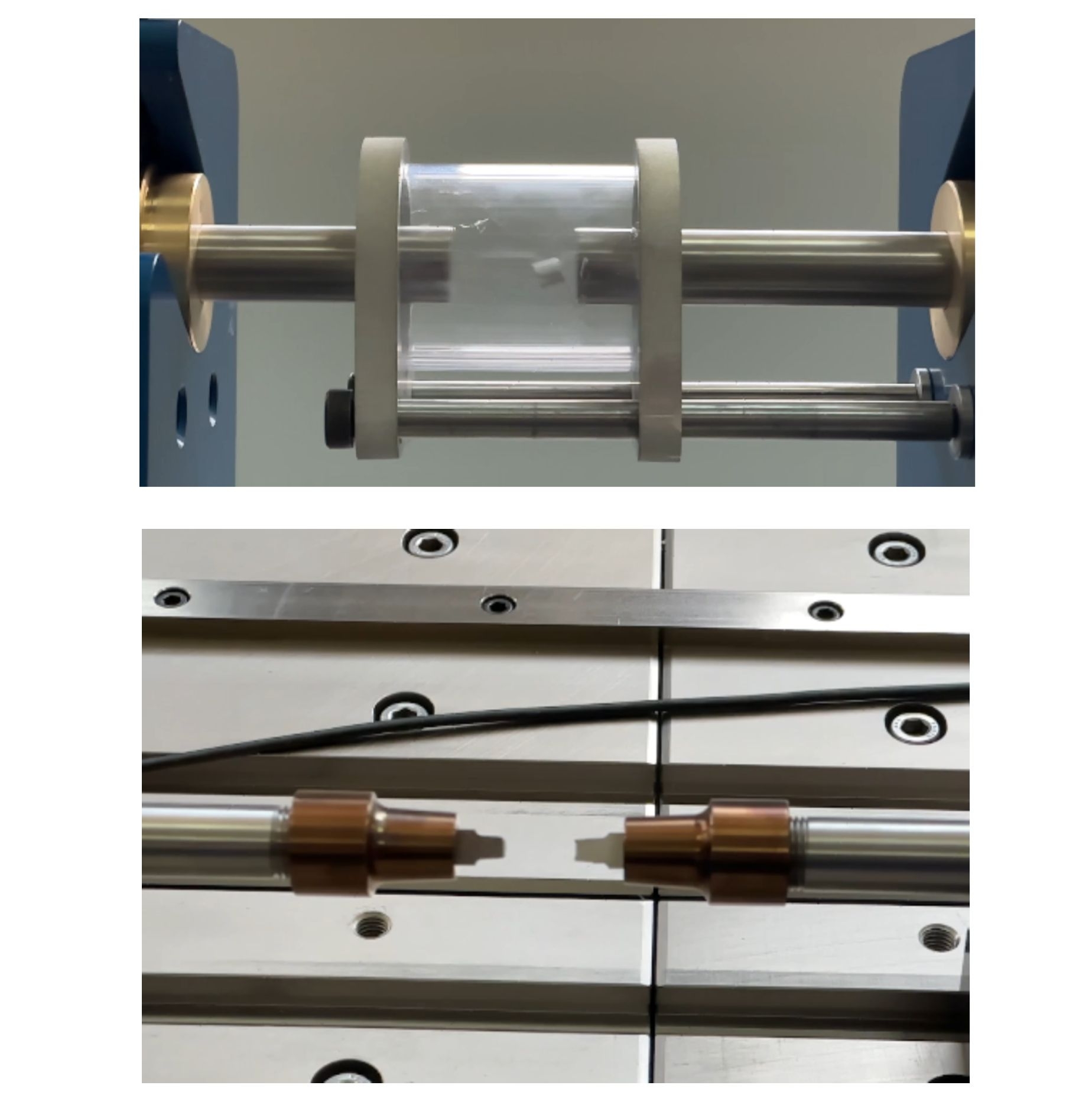
Nurol Teknoloji’s Ceramic Production Achievements and Future Investments in 2024
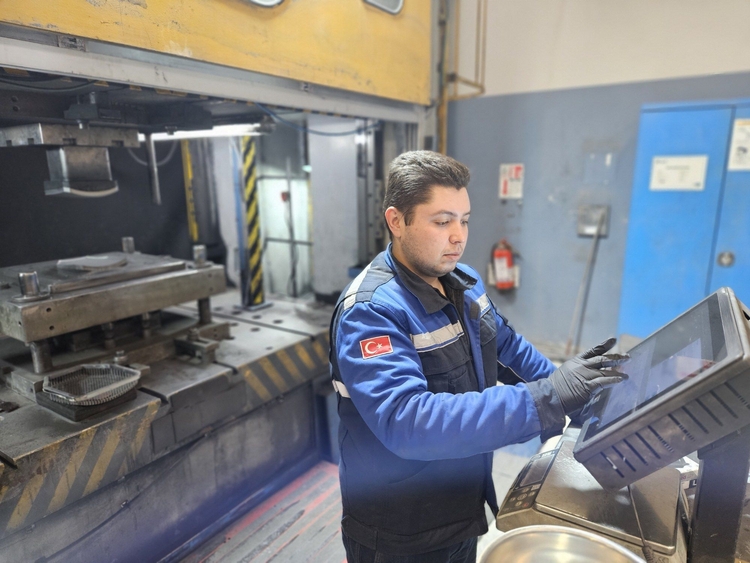
We have successfully completed the year 2024, just like the previous years. I would like to thank all my team members and colleagues who contributed to this success. Without everyone’s support, effort, and mutual trust, achieving such success would not have been possible. As Simon Sinek said, "A team is not a group of people who work together. A team is a group of people who trust each other."
In line with our vision, we continued our continuous improvement activities without slowing down. Particularly, by implementing new control parameters in our raw material preparation area, we have raised the level of quality and efficiency to a higher standard. Next year, we will continue focusing on this area and with our new investments, we aim to have a fully automated system by the end of the first quarter. This will allow us to have a more sustainable, environmentally friendly, and healthier production line.
We successfully passed the inspections and received the 'Design, Development, and Production Quality Requirements' certificate from the Ministry of National Defense, which is required for all suppliers of armies in NATO member countries.
In the final quarter of the year, we made improvements to our performance tracking system and enhanced our ability to assess individual competencies. Especially in our pressing area, with the help of our production tracking system, we enabled each operator to monitor their performance in real-time based on the parameters we set.
As part of our significant investment last year, we successfully launched our new kilns in the third and fourth quarters, together with our maintenance and repair unit, without any issues.
Next year, under the leadership of our strategic development unit, we will continue working on the automation of our production lines with further investments and efforts. We will continue to be the fastest and most reliable supplier to our glorious army and customers.
Best regards.
Murat ALGÜN / Ceramic Production Manager
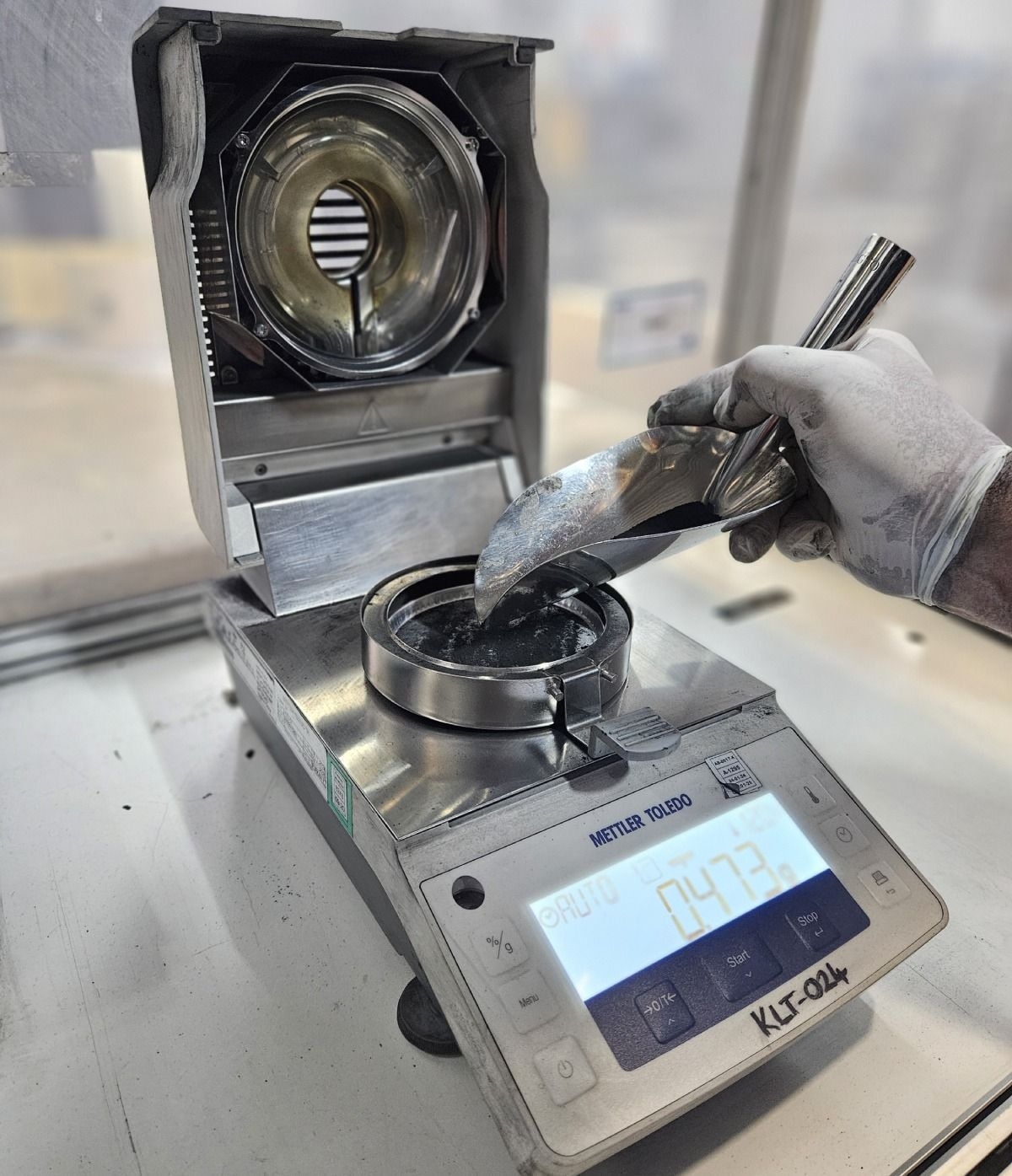
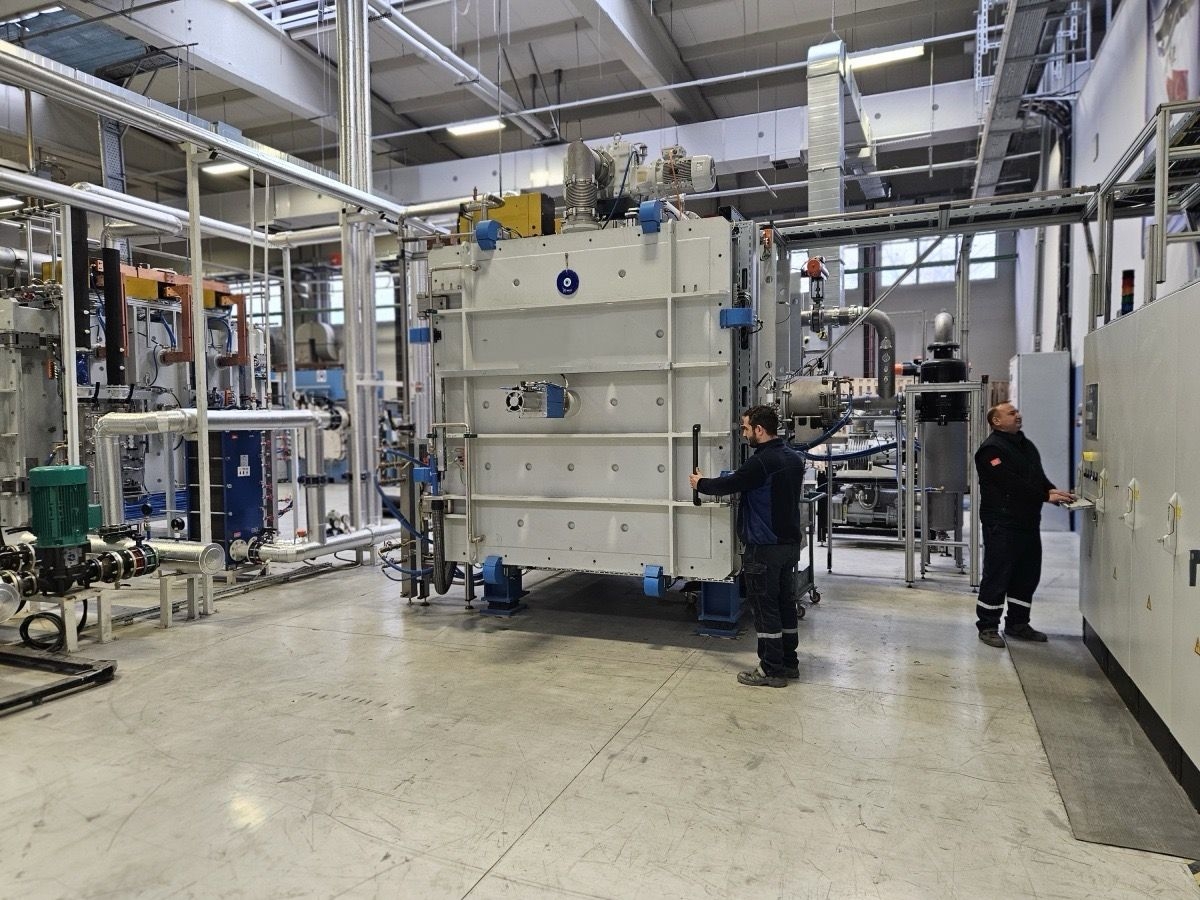
2024 Activities and 2025 Plans in the Advanced Technical Materials R&D Department
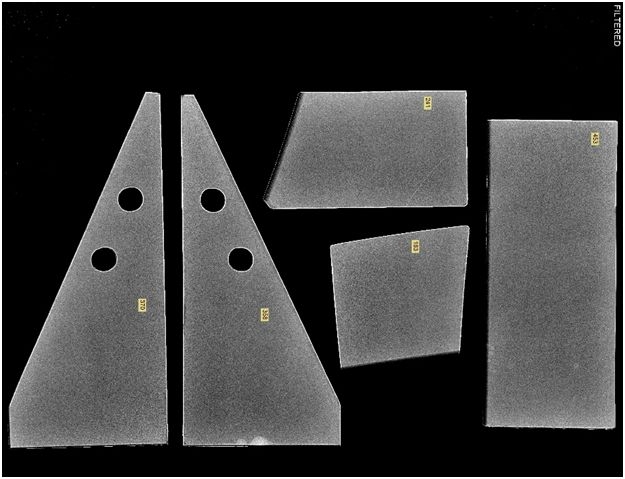
The year 2024 has been a milestone in advancing our production capabilities in the field of ballistic ceramics and contributing innovative solutions to the industry. The technologies we developed and the progress we made have strengthened our position in the sector and provided us with a strong vision for 2025.
Throughout the year, we made significant advancements in the field of fine ceramics. Specifically, we successfully produced 2-3 mm thick Silicon Carbide (SiC) and 60/40 composite ceramics for personnel chest plates. These thin structures provided excellent performance in critical requirements such as lightness and durability. Moreover, without the need for grinding operations, we succeeded in producing monolithic ceramics with very tight tolerances (e.g., 100x100 mm dimensions). These innovations enhanced the quality of both our production processes and our products.
The TAI Gökbey project marked an important turning point in the manufacturability and machinability of parts with complex geometries. We overcame challenging processes such as seat design and the machining of Boron Carbide (B4C) ceramics tailored for this design. Through this project, we once again demonstrated our capability in producing and machining complex-shaped parts and strengthened our position as a key partner in the aerospace industry.
In order to increase standardization in our manufacturing processes and better control the microstructure and mechanical properties of our products, we made significant progress in powder packaging and recipe development. By utilizing packaging models such as Furnas, we optimized products like RB Silicon Carbide, DS SiC, and RB Boron Carbide. These methods allowed us to improve the microstructure while providing greater control over mechanical properties.
The achievements we gained throughout 2024 have inspired us as we set our goals for 2025. Scaling up fine ceramics, expanding the production of tight-tolerance ceramics, and making parts with complex geometries applicable in a broader range of fields will be our primary focus. With our technology-driven innovation and quality-focused production approach, we are determined to maintain our pioneering role in the industry.
Best Regards.
Fahrettin ATAR / Ceramic and Advanced Technical Materials R&D Specialist Engineer
Halim MEÇO / Advanced Technical Materials R&D Director
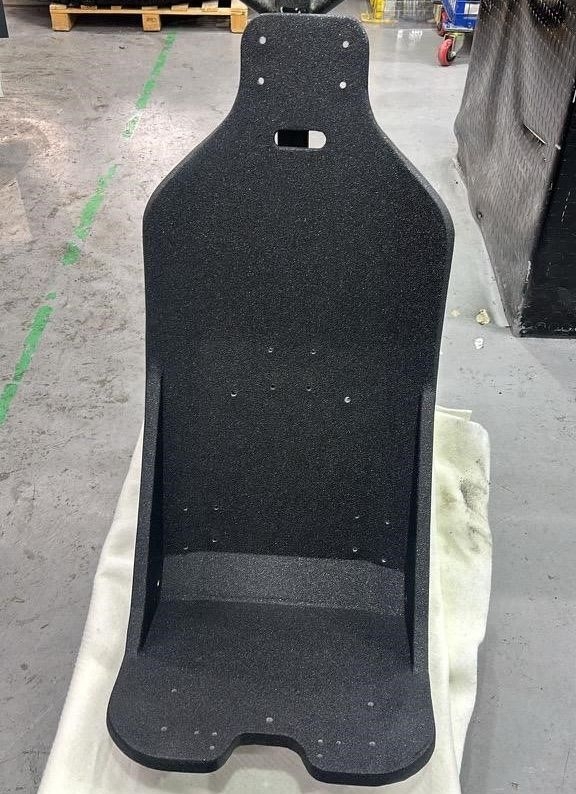
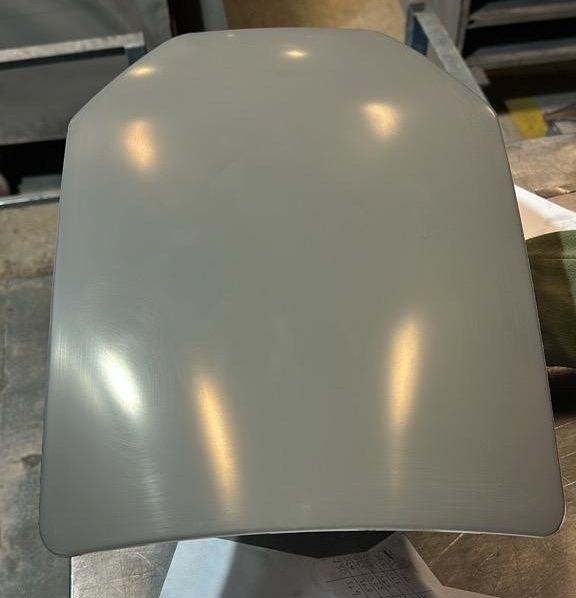